What is Carbide End Mill?
A Carbide end mill is a sort of milling cutter and cutting instrument for modern processing application. Carbide end mill can cut ever which way, even though some can’t cut transversely. It is used for making shapes and cutting process of different heavy metals in industries. End mills are utilized for processing applications like side processing, profiling, End transforming, and cutting. They are also changed the shape of things by different process like cutting and producing chips. By using this tool we can change heavy industrial metals in our desired shape. These end mills are utilized to deal with steel, cast iron, super-alloy, and non-ferrous materials. Carbide end plants can withstand higher temperature than high velocity steel apparatuses.
Manufacturing Process of Carbide Tools:
How about we see the assembling cycle of carbide?
In the first place, blend tungsten Carbide in with cobalt to make powder which can be named crude materials. The granulated blend is filled a pass on cavity and squeezed invigorates a moderate like that of chalk.
Then the squeezed compacts are set in a sintering heater and warmed at a temperature of about 1400C, bringing about solidified carbide. In the wake of sintering, the substance volume contracts extensively. Manufacturing process of carbide tools is shown in figure below.
There are many types of end mill, each suited to certain cutting applications. There are several different styles of this machine, which are commonly found in different machines:
- Smooth-face end mills
- Rough-face
- Scroll mill
- Inline mill
- Lathe end mills
- CNC end mills
- Router end mill
Smooth-face
Uses a single spinning diamond wheel on which grinding occurs, while the rough-face has two diamonds on opposite sides of the spindle. The smooth-face end mill can perform both finishing operations and drilling.
Sliding end mill
This machine is very versatile, as it can be mounted on a table, and its role is to run in conjunction with the spindle on a lathe or a mill. The sliding end mill has a fixed spindle, but its external surfaces are free of obstructions; thus, this type of end mill can slide along the edges of the workpiece. Its most common use is for cutting soft metals such as brass.
Scroll mill
A scroll mill is a similar-sized machine, but instead of using the sliding action typical of end mills, the sliding action is conducted by a helical cutter. The result is a more polished cut because the helical cutter can make accurate cuts across the width of the material. Unlike end mills, scroll cutters do not require a feed roller. The result is an accurate cut every time. These machines, though more expensive than other types of cutting machines, are suitable for heavy-duty and high-volume production.
Inline mill
An inline mill is similar to a scroll machine, but it uses a vertical rotation drill. The discs are attached to a stationary vertical spindle. To cut materials, the spindle is aligned vertically and the discs are spun in a helical pattern. As the material rotates, the discs cut and the hole is drilled. Unlike scroll machines, these machines do not need to have a feed roller and they cost less than other types of machines.
CNC end mills
The term “CNC” stands for “Computer Numbered Control.” This technology allows users to design intricate cuts using readily available software. Users simply enter the required data, which is then transferred to the machine for detailed work. The machine then controls the CNC endmill by precisely moving the spindle and other parts in and out of the cut area. The result is a cut that comes out exactly the way the user wants it.
Lathe end mills
Lathe end mills are used to perform boring tasks, such as boring a hole for a screw. The term is usually applied to these machines because they are designed to move in a similar way to a lathe. But instead of the wood being ground, or the metal inserted, the process comes down to the user manually turning a handle. The result is a more intricate design that looks like a CNC machine did it. This type of machinery is expensive and the quality of the work depends on how well the operator and the machine are used.
Plasma cutters
A plasma cutter is one of the most recent types of CNC machines and is designed to perform long-lasting cuts. It uses heat to cut materials, including plastics, metals, and ceramics. It can handle materials of any diameter, although the larger ones tend to use a larger drill. These CNC machines give the option to cut curves and hollow shapes as well as square holes and other straight lines.
Router end mill
A router machine is used most often when a router needs to cut smaller pieces, such as plates, into multiple pieces. In other words, the pieces can be produced as a whole using this machine. They make the process of producing repeated pieces much faster and easier than doing it by hand. These machines are available in different types, and you need to decide which one is best suited for your projects.
End mill in different number of flutes
There are several reasons why there are end mills on the market. They can be used for many flute types including, spools, tubular, cylindrical, tapered, and many more. The amount of material a cutter can cut in one single pass is another reason why they are so popular. You can also get them in a variety of different shapes that will give you the ability to make many flutes from a single piece of material.
Some of the things to keep in mind when purchasing your up-cut and down-cut milling machines include how often you plan on using them and if they are designed for your type of cutting. If you are only going to use the up-cut machine then you may want to consider purchasing the basic model. Some of the basic up-cut machines have a tapered design that makes them good for small jobs. If you need to make many flutes then a down-cut version will do the job. If you do not plan on making a large number of flutes, an up-cut milling machine will do the job for you.
Carbide end mills are popular for being able to cut materials. This particular device is used in a variety of different applications. Some of the most common materials that you will find cut with these types of machines are glass, plastic, metal, ceramic, wood and plaster. This device has many positive aspects to it.
The first benefit that a carbide mill offers is its ability to cut materials. No matter what you are using this machine can cut the material. This is helpful when cutting material into various shapes. This can help with making circular saws, bowls, plates, cross-sections and more. This is one reason why people prefer this over other types of cutting tools.
The two different types of carbide end mills that you can purchase are those that are powered by electricity or ones that run on either gas or propane. Both of these machines use carbide wheels along with an attachment called a center-feeder. The wheels provide the power for the cutting edges. The center-feeder is what transfers the cutting work to the grinding wheel. The power source can come from one of two different types of electrical motors: permanent magnetic motors or induction motors.
The carbide end mills 4-flute cutter is designed to be very efficient in its use. The piece can cut through any material and is also very accurate, thanks to its accurate technology. Many commercial shops that use carbide grinders often have them in use daily. The carbide cutter is also able to grind small holes and recesses, which make it perfect for the woodworking industry. Most of the commercial vendors that sell these products will provide installation services to make sure that the device is installed properly.
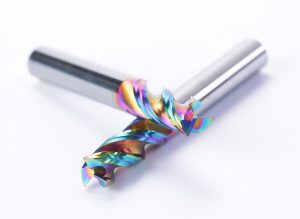
3 Flute Unequal Helix Carbide End Mills for Aluminium DLC Coated
Shapes and sizes of end mills
End mills in different shapes and sizes are important in the production of a wide range of products. Most projects will benefit from the creative application of the use of different size and shape tools. End mills are most commonly used for cutting and V-bit and ball nose cutters are most often used for finishing processes. There are also end versatile mills. These include a stepover tool and a sliding stepover.
1. A stepover; is a type of milling tool that has a single continuous stroke that allows it to cut through the wood by using little wear and tear. A slide-over machine allows you to cut long runs of material on a single pass. A combination of these two machines offers versatility when it comes to carbide end mills. Both carbide and diamond are common materials that are used to make end mills.
2. Flat ends; are designed to cut curves. Cylindrically curved cuts are a little bit difficult to perform than round cuts because of the flat top of the material. End mills in different shapes and sizes are commonly used to perform this type of cutting. End mills in different numbers of heads give you flexibility when making more pieces of a single piece of material.
Advantage of end mill:
If you have a larger budget then you may want to consider purchasing the ultimate end mills known as the g-wizard. These machines come with a multitude of features and capabilities that are designed to meet the needs of any craftsman or woman that is serious about their work. If you purchase these machines, they will allow you to create beautiful music in a short period. Once you master the technique, it is easy to create music by holding the stylus against the sound source.